Vertical translational movement of the rod of the Regulating Organ (Regulator - RO) of the
water-water energetic reactor
provides the electric drive in the form of a Stepped Electromagnetic Drive (SED).
Measuring the position of the forward-moving rod of the RO is a prerequisite for the safe and efficient operation of the reactor.
Electric actuators SED-3 and SED-2 used at nuclear power plants are equipped with Rod Position Sensors (RPS)
that generate position signals due to sensitive organs that have mechanical connection to the moving rod.
Drive SED-3
has a RPS, fixing each step and determining the position of the rod with a discrete step.
The sensor works in cramped conditions at elevated temperature and is practically unavailable for mechanical maintenance and repair.
Drive SED-2 has a RPS, which determines the position of the rod with a resolution of 350mm (does not respond to each step).
It also operates in cramped conditions at elevated temperatures and is also not readily available for mechanical maintenance.
Reduced accuracy and inability to fix each step prevent more efficient maintenance of the technological process and
account for the resource of the electric drive.
Creating a simple device that could parry these disadvantages of position sensors
and to a certain extent would reserve their functions is an urgent task.
During 2003-2006, I carried out research work on this topic, which resulted in the creation of prototypes of the Step Control Sensor (SCS)
for the drives of SED-2 and SED-3, operating on the basis of other principles. Real-time measurements and processing of current and
voltage signals of pulling PM, locking LM and fixing FM electromagnets are conducted. The consequence is the issuance of a message
about the done or not done step before the end of the schedule.
The following tasks were accomplished:
• Development of the layout of the SED, consisting of one pulling electromagnet and Control Unit CU1.
This electromagnet provides lifting and lowering of the inner rod, as in the current cyclogram corresponding to the upward movement,
as well as in the current pattern corresponding to the downward movement. On the rod it is possible to set the load to 30 kg
(large ones have not been tested). The design of the electromagnet makes it possible to "jam" the rod, i.e. do not allow it to move
when applying currents to it corresponding to one of the cyclograms.
• Development of a Module of Voltage Sensors MVS01 and a Module of Current Sensors MCS01 based on the sensors of the
Swiss company "LEM".
These sensors allow the conversion of voltages and currents into proportional voltage signals acceptable for the ADC level.
• Development of the “E-440 TESTER” software and hardware system based on a laptop, the
L-Card E-440 ADC module (new name: E14-440),
connected to the laptop via an external USB1.1 bus, MVS01, MCS01 and a program that allows processing, saving and reproducing measurement results.
• Measurement and processing of results: on the layout of the drive, on SED-3 in
OKB "Gidropress" and on SED-2 at
Kalinin NPP.
Consequences of these studies were the test reports and the 1st and 2nd versions of the Step Control Sensor algorithm.
• Theoretical studies of pulling electromagnets of SED-2 and SED-3 drive (flux linkage, inductance, force of attraction, EMF).
Analysis of the interaction of the mechanisms of SED.
• Creation of the final version of the Step Control Sensor algorithm, taking into account the work of all three magnets and
the release of the technical report on the research done.
• Development of a control program for the
Fastwel RTU188-BS
microcontroller, which allows to determine the implementation of the step before the drive completes all operations for its completion.
• Modification of the "E-440 TESTER" hardware and software complex to the level allowing real-time SCS functions to be performed and
to display a message about the step taken or not made before the end of the schedule with graphical display of the step feature or its absence,
and also allowing to emit the operation of the SED due to playback through the DAC of previously recorded voltage and current signals on PM, LM and FM.
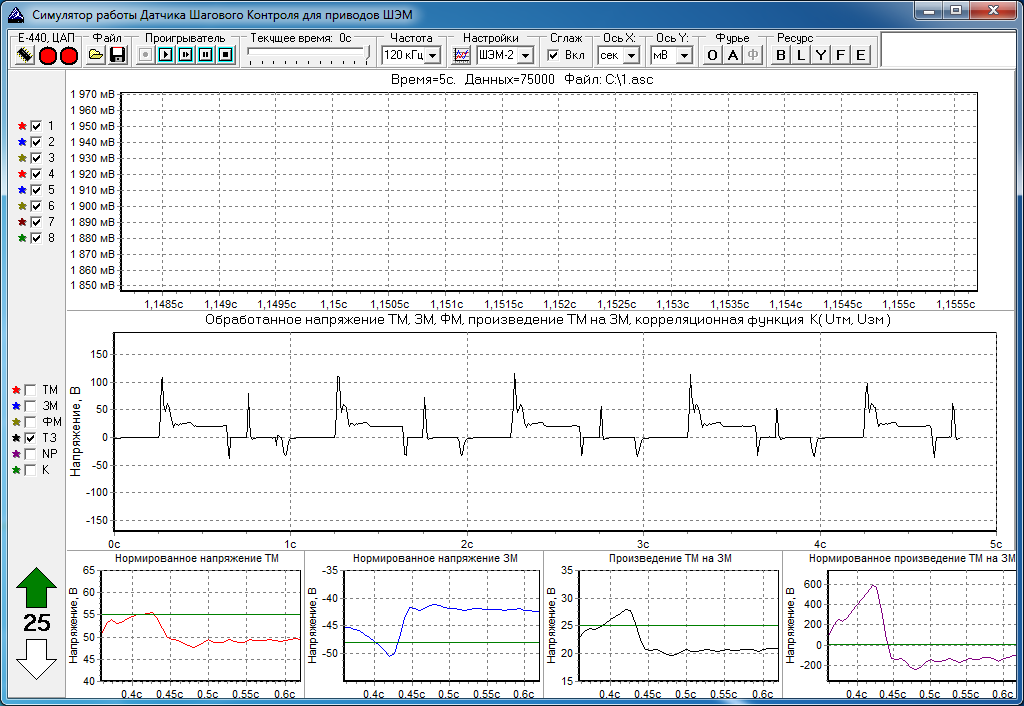
• Development of a technique for real-time induction, winding resistance, temperature of electromagnets, rod travel time and magnitude of induced EMF.
• Development of the principle of constructing the Hardware and Software Complex "Diagnostics System" on the basis of SCS,
integrated into an industrial network based on the RS-485 interface, and the development of a technical task for the Kalinin NPP,
where the customer is RosEnergoAtom.
At present, this work is completed. Patent for invention No. 2353989 has been received.
At any time, according to the customer's requirements, this system can be delivered in the required configuration.
The scanned copy of the patent in Russian: Patent.jpg
The full text of the patent in Russian: Patent.pdf
Article from "Sensors and Systems 2006": SHS_DS.doc.zip
Article from "Electrical Engineering" for 12.2006: SHS_DS2.doc.zip